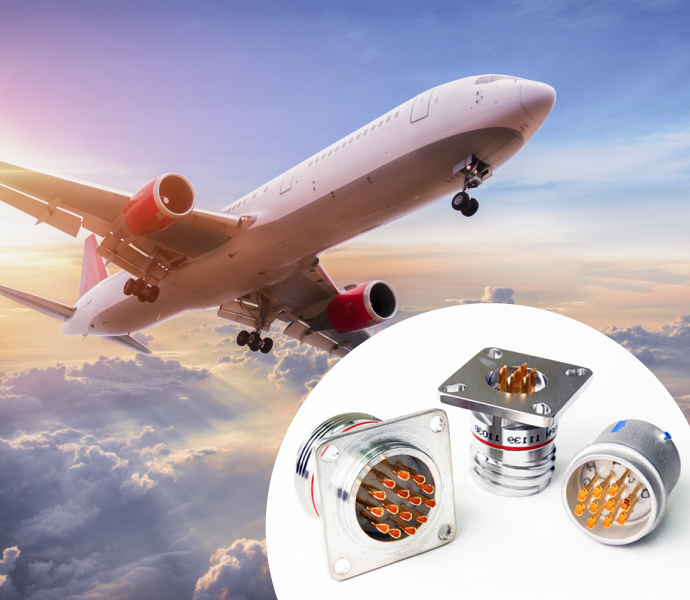
When equipment faces extreme conditions such as high altitudes, varying atmospheric pressures, severe weather, and rapid temperature changes, as in aerospace, ensuring the integrity and reliability of electronic connections is paramount. That’s where hermetically sealed connectors come in.
Uses for Hermetic Connectors
The primary purpose of hermetically sealed connectors is:
- to provide absolute protection against the ingress of air or other gases
- waterproofing
- sealing pressure differentials reliably
- safeguarding against aggressive media in hazardous environments (ATEX)
Hermetically sealed connectors conforming to MIL-STD (military standard) or MIL-SPEC are standard in these industries, ensuring robust design and reliability. Moisture protection is crucial for sensor applications, making hermetic connectors indispensable for sensor amplifier electronics. These connectors find extensive use in military and aerospace applications where they shield electronics from diverse environmental challenges, but can also play a pivotal role in vacuum electrical feed-throughs for high-vacuum or ultra-high-vacuum applications.
Hermetic Seals in Aerospace and Satellites
Hermetic seals are indispensable for various critical components, protecting against temperature fluctuations, humidity, contamination, high pressures, and vibrations. Common applications that require hermetic seals:
- Laser systems for satellites
- Power supply systems
- Turbine control
- Lighting
- Ventilation management
Hermetic Connector Sealing Methods
How are hermetic seals created?
Hermetic seals are typically created using glass-to-metal or ceramic-to-metal sealing for high durability or epoxy for cost-efficiency. Advanced techniques like compression, welding, and cold welding are also employed, each chosen based on the seal’s required strength, environmental resistance, and material compatibility.
Glass-to-Metal Sealed Connectors
Considered the “gold standard” for hermetically sealed connectors, glass-to-metal sealed connectors utilize glass for electrical insulation and hermetic sealing. The manufacturing process involves specialized furnace equipment at high temperatures. The reliability of glass seals is exceptionally high, maintaining hermeticity over extended periods. These connectors excel in withstanding high-pressure differentials, elevated temperatures, and physical robustness. However, design constraints and material limitations must be considered.
Ceramic-to-Metal Sealed Connectors
Ceramic-to-metal sealing, involving ceramics like alumina and a brazed metallic layer, is a high-end technology with superior performance in specific applications. It offers resistance to thermal and mechanical shocks and can sustain higher application temperatures. Despite its advantages, the manufacturing process of these hermetically sealed connectors is costlier compared to other methods.
Epoxy or Silicone-based Polymer Sealed Connectors
One of the sealing methods for hermetically sealed connectors involves potting with epoxy resins or silicone-based compounds. This technique, though relatively simple and adaptable to various production environments, has limitations in achieving the hermeticity levels provided by other methods. The higher diffusivity of gases and moisture through polymer seals, along with potential absorption and outgassing, makes this method less suitable for certain demanding applications.
Key Takeaways:
- Hermetically sealed connectors conforming to MIL-STD (military standard) or MIL-SPEC are standard in these industries, ensuring robust design and reliability.
- Hermetic seals are typically created using glass-to-metal or ceramic-to-metal sealing for high durability or epoxy for cost-efficiency.
- Hermetic seals are indispensable for various critical components, protecting against temperature fluctuations, humidity, contamination, high pressures, and vibrations.
- One of the sealing methods for hermetically sealed connectors involves potting with epoxy resins or silicone-based compounds.
- Considered the “gold standard” for hermetically sealed connectors, glass-to-metal sealed connectors utilize glass for electrical insulation and hermetic sealing.
- Ceramic-to-metal sealing, involving ceramics like alumina and a brazed metallic layer, is a high-end technology with superior performance in specific applications.
The Air Electro Hermetic Connection
Hermetic connectors are the guardians of electronic integrity in aerospace, providing robust protection against harsh environmental conditions and challenges. Understanding the different sealing methods ensures the reliability and longevity of electronic connections in critical applications.
The choice between sealing methods depends on the specific requirements of the application. Air Electro stands at the forefront of hermetic connector technology, offering a diverse range of connectors encompassing circular to d-subminiature designs. Our hermetic connectors adhere to rigorous military specifications such as MIL-DTL-38999, MIL-DTL-26482, MIL-DTL-83723, MIL-DTL-24308, MIL-DTL-5015, and also include custom-designed options.
We’re committed to providing reliable and specialized hermetic connectors that meet the stringent requirements of various applications, particularly in the military and aerospace sectors. Choose Air Electro for a seamless and reliable connection that stands the test of time. Start today.